New smart factories capture all the attention, but the reality for most manufacturers is to modernize existing facilities.
Investing in new equipment is often not a viable option.
Digital transformation does not require completely replacing the production infrastructure.
By strategically integrating digital capabilities into legacy systems, manufacturers can achieve remarkable improvements without massive capital expenditures. This approach allows existing investments to be preserved while embracing innovations from Industry 4.0. By analyzing processes and optimizing flows, companies strengthen the resilience of their supply chains. The future of production lies in this symbiosis between tradition and modernity.
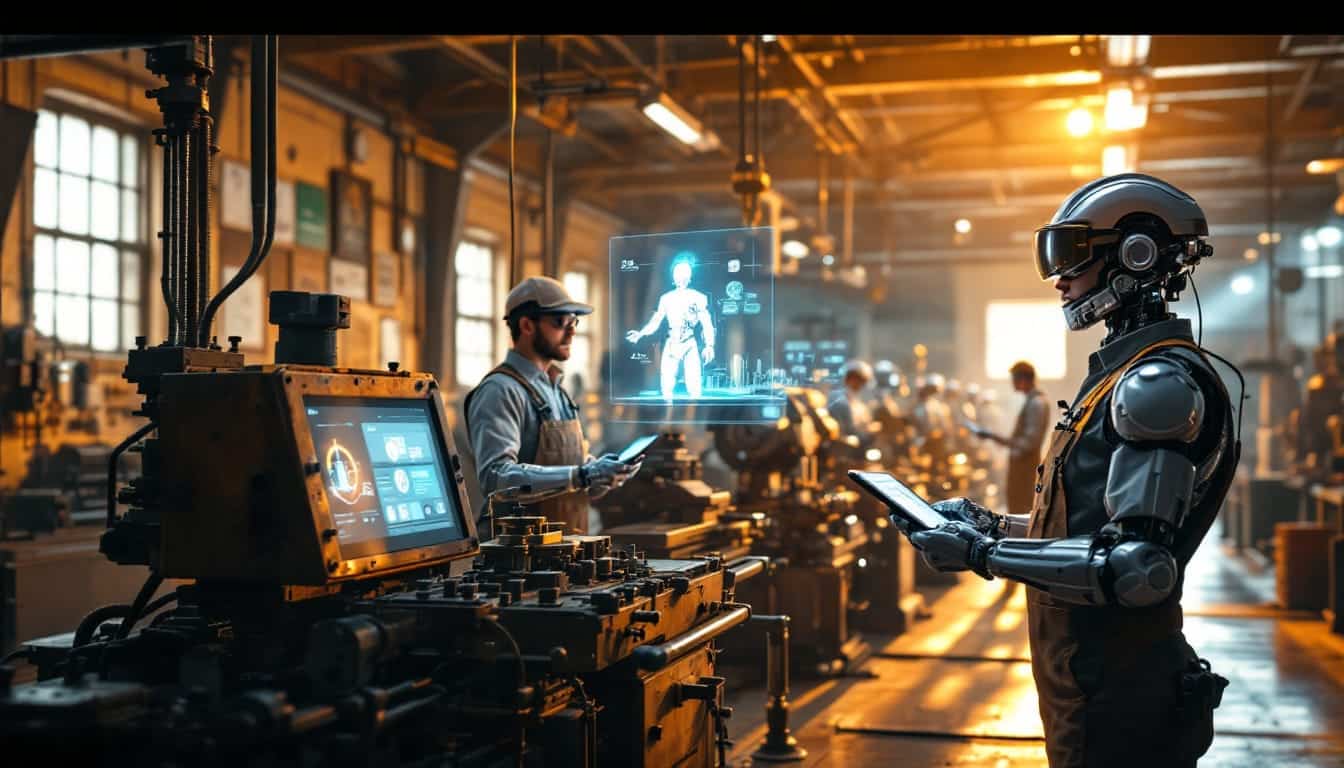
In today’s industrial landscape, adopting Industry 4.0 has become a necessity to remain competitive. However, the reality for most manufacturers lies in modernizing existing facilities without being able to simply replace old equipment. This article explores a pragmatic approach to integrating advanced technologies while valuing existing infrastructures.
Table des matières
ToggleWhy is modernizing existing infrastructure essential?
New smart factories often receive all the attention, but the majority of manufacturers must find ways to modernize their current facilities with equipment investments they cannot simply discard. The good news? Digital transformation does not require the complete replacement of production infrastructure. By strategically integrating digital capabilities into existing systems, manufacturers can achieve remarkable improvements without massive capital expenditures.
During a visit to a large automotive components factory in the Midwest, I observed equipment from the 1980s operating alongside systems from the 2010s. The operations manager expressed a common sentiment: “We cannot justify scrapping equipment that still produces quality parts simply because it is not connected.”
This perspective is economically prudent and environmentally responsible, in line with Deloitte’s research on sustainable manufacturing practices. The question becomes: how to bridge the gap between legacy infrastructure and the promise of Industry 4.0? According to a study by the Manufacturing Leadership Council, over 70% of manufacturing equipment in North America is over 20 years old. This installed base represents billions in capital investments and contains decades of embedded procedural knowledge.
What strategies to adopt to integrate old equipment?
Integrating old equipment into Industry 4.0 requires specific strategies. Here are three key approaches:
1. Sensor retrofitting: the digital nervous system
The foundation of any digital transformation is data. Modern IoT sensors can be applied non-invasively to monitor equipment conditions without requiring significant modifications to existing machines, as demonstrated by McKinsey’s research on IoT applications in manufacturing.
A precision metal components manufacturer I collaborated with installed wireless vibration sensors on 1990s CNC machines for less than €500 per machine. This simple addition enabled them to detect signs of bearing wear two weeks before a failure, shifting from reactive to predictive maintenance and reducing unplanned downtime by 37%.
The key lies in a clear understanding of the information that would lead to significant improvements. Ask yourself: What critical parameters, if monitored, would provide actionable insights?
2. Edge computing: intelligence at the source
Small industrial computers can be installed near equipment to collect, process, and act on data without requiring equipment replacement. For example, a paper product manufacturer added compact edge computers to its converting lines to analyze subtle variations in product weight in real-time. The system could detect drift conditions and automatically adjust machine settings, thus reducing material waste by 8.2% without replacing any major equipment.
Edge computing also allows facilities to start their digital transition without waiting for complete IT infrastructure upgrades, a strategy recommended by the Manufacturing Enterprise Solutions Association (MESA) in their guidelines for implementing Industry 4.0.
3. Middleware solutions: building digital bridges
Modern middleware platforms designed for manufacturing environments can extract data from legacy protocols and translate it into formats compatible with contemporary systems. A food processing company used such middleware to connect 1990s PLCs to their modern MES system. Instead of replacing functional equipment, they invested in software capable of communicating across these technology generations, resulting in a unified digital thread providing real-time visibility across their operations for about 15% of the cost of replacing equipment.
To learn more about manufacturing automation and the competitive advantages of Italian robotic equipment, check out this article.
How to identify high-value modernization opportunities?
Not all legacy equipment deserves equal investment in digital capabilities. Prioritization requires a structured approach focused on three key dimensions:
1. Critical path analysis
Start by mapping your production systems to identify the true bottlenecks and critical path operations. Equipment that dictates the overall throughput of your facility should be prioritized for digital improvement. A comprehensive assessment should include:
- Impact on production: volume affected by the equipment
- Impact on quality: potential for generating defects
- Flexibility limitations: constraints on production changeovers
- Maintenance history: reliability concerns
For a medical device manufacturer facing inconsistent throughput, this analysis revealed that while their aging molding machines received the most attention in maintenance, it was actually their assembly systems that limited production. By digitizing assembly equipment first, they achieved a 23% throughput improvement with minimal capital investment.
2. Data value assessment
Before proceeding with retrofitting, assess the potential data value of each system. Ask yourself the following questions:
- What decisions will this data inform?
- How quickly will we need this information to act meaningfully?
- What is the economic impact of owning this information?
A chemical processor initially planned a full deployment of sensors on all reactors. After assessing the data value, they determined that monitoring only three parameters on their most variable processes would provide 80% of the potential improvements. This targeted approach reduced their initial digital investment by 65% while enabling critical process enhancements.
To learn more about educational initiatives in Industry 4.0, discover the launch of the Industry 4.0 Academy by NCPA and Penn State DuBois.
3. ROI-oriented implementation
Unlike greenfield deployments where digital capabilities are integrated from the start, brownfield transformations must justify each improvement. Develop clear return on investment (ROI) models for retrofitting options, including initial investment, recurring costs, expected benefits, and implementation risks, as recommended by the Boston Consulting Group in a 2022 paper on digital transformation in manufacturing.
A discrete manufacturer created a phased implementation approach where only retrofits with a projected ROI of less than 12 months were approved during the first phase. This disciplined approach built organizational confidence as initial projects delivered clear results, creating momentum for subsequent phases.
What are the benefits of the brownfield approach?
While many see existing infrastructure as a constraint for digital transformation, it can actually offer advantages. Brownfield facilities have established processes, experienced workforces, and proven production capabilities. Digital enhancement leverages these strengths rather than abandoning them.
Organizations that successfully transform their brownfield operations gain the benefits of Industry 4.0 – improved visibility, increased flexibility, optimized maintenance, and data-driven decision making – all while leveraging existing capital investments. The result is a digital transformation that delivers quick returns while creating platforms for future innovation.
For example, Hyundai’s mega factory in Georgia successfully propelled Industry 4.0 by integrating advanced technologies into their existing facilities, demonstrating that complete replacement is not always necessary.
How to plan a technology roadmap for gradual transformation?
The most successful brownfield transformations unfold as planned journeys rather than one-off events. A well-structured roadmap should include:
1. Capability-based planning
Rather than solely focusing on technological implementation, successful roadmaps define the capabilities the organization needs to develop:
- Phase 1: Achieving real-time visibility into production status and performance
- Phase 2: Enabling condition-based maintenance for critical equipment
- Phase 3: Implementing closed-loop quality control systems
- Phase 4: Activating dynamic production scheduling
This approach allows technologies to evolve over the implementation period while maintaining a focus on commercial capabilities that bring value.
2. Developing a layered architecture
Build your digital infrastructure in well-defined layers that can evolve independently:
- Connection layer: Physical sensors, data acquisition, and basic connectivity
- Data management layer: Storage, normalization, and basic processing
- Application layer: Analytics, visualization, and user interfaces
- Integration layer: Connectivity of enterprise systems and information flows
This architectural approach enables manufacturers to start with targeted improvements while ensuring future compatibility as systems mature.
Discover how Gymd, a Chinese technology company, is driving Industry 4.0 in Malaysia through its engagement in the automotive sector in this article.
3. Integrating skills development
The most neglected aspect of brownfield transformation is human skills development. Effective roadmaps include parallel tracks for technology and skills:
- Technical training: to support new systems
- Change management: to encourage adoption
- Process development: to capitalize on new capabilities
- Leadership development: to manage digitally enabled operations
A heavy equipment manufacturer paired each phase of its technological implementation with corresponding training programs. This simultaneous development ensured that new capabilities were fully utilized as soon as they became available.
To delve deeper into adapting to Industry 4.0 and intralogistics automation, listen to our dedicated podcast.
What are the concrete benefits of brownfield transformation?
While many manufacturers view existing infrastructure as a limitation, it can actually offer significant advantages. Brownfield facilities benefit from established processes, experienced workers, and proven production capabilities. Digital enhancement leverages these strengths, thus avoiding abandoning them.
Organizations that successfully transform their brownfield operations reap the benefits of Industry 4.0 – enhanced visibility, increased flexibility, optimized maintenance, and data-driven decision making – all while leveraging existing capital investments. The result is a digital transformation that generates quick returns while creating foundations for future innovation.
For instance, the mega factory of Hyundai in Georgia demonstrated how the integration of advanced technologies into existing facilities can propel Industry 4.0 without necessitating a total replacement of equipment, thereby highlighting the effectiveness of a pragmatic approach.
Industry 4.0 does not require the replacement of everything that existed before. Through thoughtful integration, strategic prioritization, and a capability-based roadmap, manufacturers can transform their operations one improvement at a time – achieving digital excellence without starting from scratch, as highlighted in the World Economic Forum white paper on digital transformation in manufacturing.