Imagine a revolution in the world of athletic performance: custom insoles for Olympic athletes created in record time. This is now possible thanks to Asics’ innovative technology, offering quick and tailored printing in under an hour. Discover how this major advancement will change the game for high-level athletes.
Table des matières
ToggleA revolution for the sports world
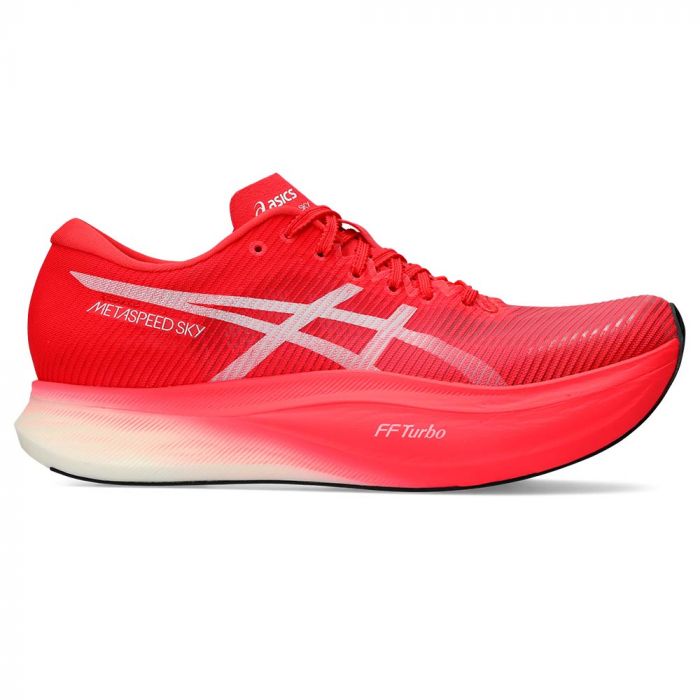
With its mobile 3D printing studio, Asics is shaking up the sports world by allowing the printing of custom insoles in less than an hour. In partnership with Dassault Systèmes, the Japanese multinational is offering this innovation to elite athletes, with the aim of making it accessible to the general public.
A promising partnership
For the 2024 Paris Olympic and Paralympic Games, Asics and the 3D design software publisher Dassault Systèmes are introducing this revolutionary technology. The mobile studio, located at Dassault Systèmes’ facilities in Vélizy (Yvelines), is set to evolve as sporting events approach.
Custom insoles for Novak Djokovic
Currently, the studio is used to equip the shoes of Novak Djokovic, the tennis champion and official partner of Asics. Djokovic uses these custom insoles nearly every day during matches. According to Mitsuyuki Tominaga, CEO of Asics, this innovation helps prevent injuries by correcting athletes’ pressure points.
A simple and quick process
The process begins with a scan of the athlete’s bare feet using a mobile application developed by Asics. This app takes four photos to measure each foot from all angles, using artificial intelligence. The scan is then sent to software developed by Dassault Systèmes for automated processing. The result is a point cloud detailing the geometry and pressure points of the foot.
3D insole manufacturing
The data is then used to model the insoles in polymer, which are manufactured in a 3D printer. The entire process, from scanning to production, is overseen thanks to the digital twin of the mobile unit. This modeling work, which Asics and Dassault Systèmes collaborated on for 18 months, represents a significant technical breakthrough.
Customization for performance
Once modeled, the insole is manufactured, dried, and heated to ensure optimal durability. This process also allows for the production of recovery sandals, which are in high demand by athletes. Asics has already sold 30,000 pairs of these sandals, although the release date for the custom insoles has not yet been announced.
- Quick and accurate scan with a mobile app
- Data processing by advanced software
- Manufacturing in under an hour thanks to 3D printing
A rapidly evolving market
The market for custom 3D printed insoles is rapidly expanding. Companies like Adidas are also exploring this avenue to offer even greater personalization. While the challenge is significant, the collaboration between Asics and Dassault Systèmes demonstrates that constant innovation can open new avenues for athletes and the general public.
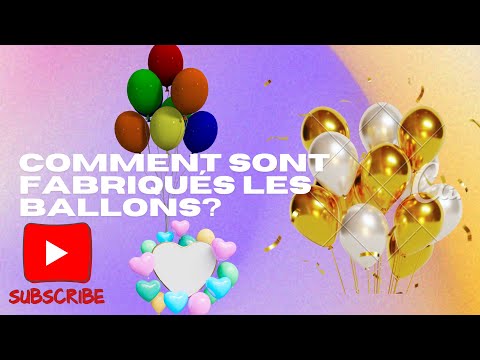
Quand je vois et j'écoute ça, je pense au paillasson en effet.
— Léopold Saroyan (@cf_deTartas) April 3, 2024
Un paillasson qui en a vu passer des semelles voulant tant bien que mal en ressortir propres.
C'est exactement l'impression que donne cet individu qui représente tout sauf la France.#LouisBoyard https://t.co/2hoVnspT6x