Welcome to our secure platform.
We have noticed unusual activity associated with your connection.
To ensure optimal navigation, please follow the instructions below.
If you are using an anonymous proxy, please disable it and try again. If the error persists, please contact our customer service mentioning the following incident number: b2012ca8-cy3y-434f-8ae4-10aa1f16e7cb. In the meantime, you can continue browsing by clicking the “I am human” box. Thank you for your understanding.
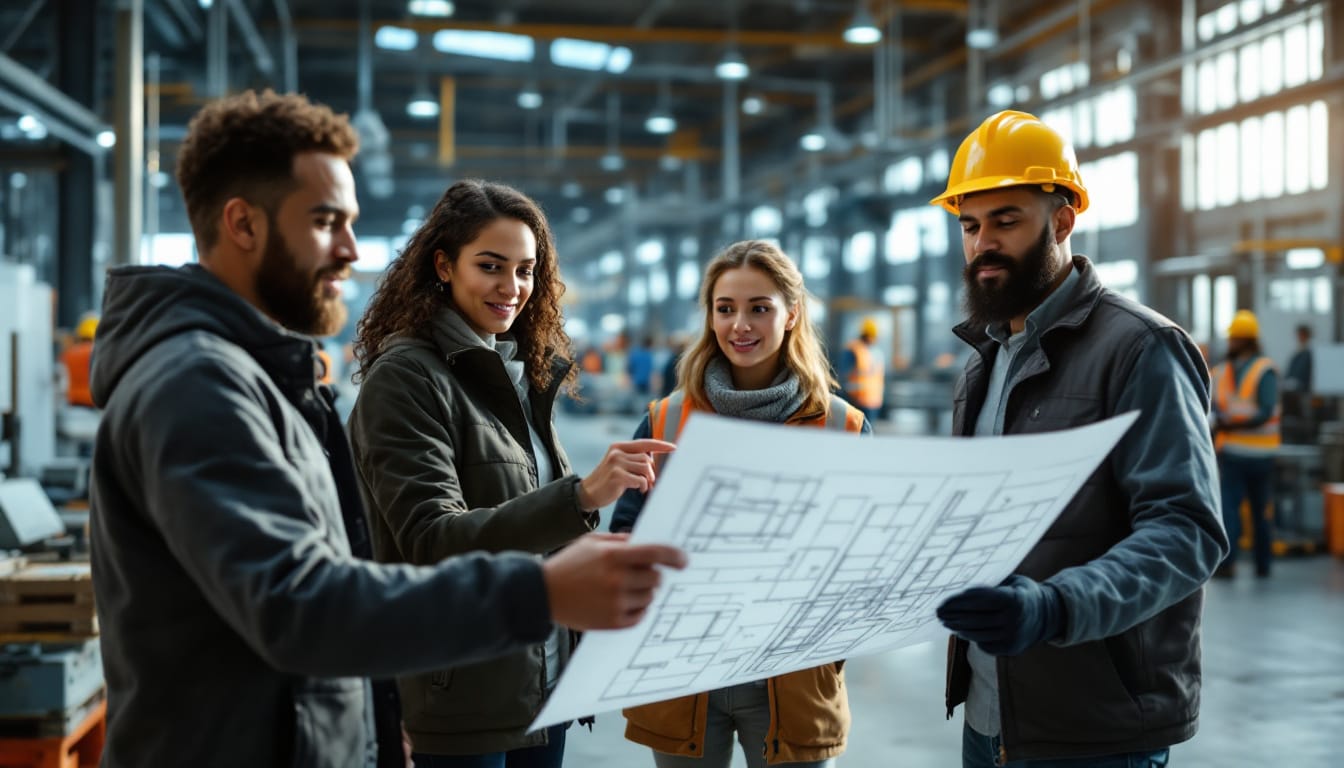
“`html
Table des matières
ToggleUnderstanding the Initial Challenges of Industrial Startups
Launching an industrial startup represents an exciting adventure, but it is fraught with pitfalls, especially during the establishment of the first factory. Entrepreneurs must navigate through a multitude of challenges, ranging from infrastructure design to the integration of advanced technologies. For example, Orius, the Toulouse-based startup has succeeded in revitalizing traditional industrial processes by reintroducing natural elements, thus illustrating the importance of innovation in this sector.
One of the main challenges lies in the implementation of effective cyber-physical systems. These systems, which combine physical and digital components, are essential for optimizing operations and ensuring smooth production. Furthermore, the adoption of cloud technologies allows for better data management and increased flexibility, thus facilitating real-time decision-making.
Moreover, a deep understanding of industrial processes is crucial. Startups need to analyze and optimize every stage of production to ensure quality and profitability. Articles like the one on industry 4.0 in the United States and China highlight how global leaders adapt their strategies to remain competitive in this digital era.
One of the levers to overcome these challenges is the development of a well-thought-out digitalization strategy. This involves not only the integration of technologies but also the training of teams and the adaptation of internal processes. Leaders must ensure that every team member is aligned with the digital objectives to foster successful transformation.
Finally, the ability to provide concrete solutions to the issues of industry 4.0 distinguishes successful startups. By focusing their efforts on pragmatism and efficiency, they can adequately respond to the specific needs of the market, thus ensuring their growth and sustainability.
What are the Main Technological Obstacles in Creating a First Factory?
Technological obstacles are often at the heart of the difficulties encountered by industrial startups when creating their first factory. One major challenge is the integration of automated systems, which requires specialized expertise and significant investments. For example, The Exploration Company had to overcome technological barriers to develop reusable capsules intended for space exploration, illustrating the complexity of ambitious projects.
The compatibility of existing technologies with new solutions is another key obstacle. It is essential to ensure that different technical components can work together harmoniously. This often involves phases of testing and adjustments to guarantee smooth integration.
Additionally, the security of digital systems is an increasing concern. With the rise of cyber threats, startups need to invest in robust protective measures to secure their data and operations. Implementing advanced security protocols is essential to prevent intrusions and data losses.
Finally, the high cost of cutting-edge technologies can represent a significant barrier. Startups often have to juggle limited budgets while trying to adopt innovative solutions. This requires rigorous financial planning and the search for adequate funding to support technological investments.
How to Optimize Resource Management in a First Factory?
Optimizing resource management is crucial for the success of a first factory. Effective management allows for maximizing productivity while minimizing costs. One of the first steps is to analyze existing processes to identify inefficiencies and opportunities for improvement.
The adoption of integrated management systems, such as ERPs (Enterprise Resource Planning), can greatly facilitate this optimization. These systems allow for better coordination between different departments, thereby ensuring a more efficient use of material and human resources.
Moreover, automating repetitive and time-consuming tasks helps free up time for employees, allowing them to focus on higher value-added activities. The integration of intelligent technologies, such as artificial intelligence and the Internet of Things (IoT), can also provide valuable insights for decision-making.
Continuous training of teams is another essential aspect. By investing in the development of their employees’ skills, startups can improve productivity and ensure better adaptation to new technologies.
Finally, proactive inventory management is essential to avoid stockouts or surpluses. By using advanced forecasting tools, companies can anticipate material needs and adjust their production accordingly, ensuring a smooth and responsive supply chain.
What Strategies to Adopt for Successful Digitalization?
Digitalization is a fundamental element for industrial startups looking to modernize their operations. A successful strategy begins with a thorough assessment of the company’s needs and objectives. It is crucial to clearly define what one hopes to achieve through digitalization, whether it be improving productivity, reducing costs, or product innovation.
Next, the selection of appropriate technologies plays a determining role. Companies need to choose technological solutions that integrate well with their existing systems and meet their specific needs. For example, integrating cloud platforms can offer increased flexibility and better data management.
Training and engagement of employees are also essential for ensuring a smooth adoption of new technologies. Teams must be well-informed and trained to effectively use digital tools, which often requires ongoing training programs and continuous support from management.
Additionally, it is important to set performance indicators to measure the impact of digitalization. These KPIs (Key Performance Indicators) allow for tracking progress and adjusting strategies based on the results obtained.
Finally, clear and transparent communication throughout the digitalization process fosters buy-in from all stakeholders. By involving employees in the process and valuing their contributions, startups can create an environment conducive to innovation and digital success.
What Lessons Can Be Learned from Successful Industrial Startups?
Analyzing the feedback from successful industrial startups offers valuable lessons for new companies. Cases like Ynsect and Northvolt demonstrate that a clear vision and constant adaptation to market challenges are essential for thriving.
One of the main lessons is the importance of continuous innovation. Successful startups constantly invest in research and development to stay at the forefront of technologies and anticipate market changes. This approach enables them to offer unique solutions and differentiate themselves from the competition.
Flexibility and organizational agility are also crucial. Companies must be able to rapidly adapt to changes and pivot when necessary, whether in response to new opportunities or unexpected obstacles.
Furthermore, collaboration and strategic partnerships play a key role in the success of industrial startups. By working closely with technology partners, suppliers, or even competitors, companies can share resources, knowledge, and expertise, thereby strengthening their market position.
Finally, rigorous financial management and strategic planning are essential. Startups need to ensure they maintain healthy cash flow, manage their investments effectively, and plan their growth sustainably.
What is the Market Projection for Industry 4.0 in North America?
The market for industry 4.0 in North America is experiencing rapid growth, with forecasts indicating it could reach $18,962 billion by 2032. This expansion is primarily driven by the increased adoption of digital technologies, such as artificial intelligence, the Internet of Things (IoT), and advanced robotics.
North American companies are investing heavily in the automation and digitalization of their processes to improve productivity and reduce operational costs. This trend is supported by a growing demand for customized products and flexible production, thereby meeting the expectations of modern consumers.
Moreover, the emphasis on sustainability and energy efficiency plays a crucial role in the development of industry 4.0 in North America. Companies are seeking to integrate environmentally friendly solutions into their operations, thereby contributing to a reduction of their carbon footprint and promoting sustainable practices.
Government policies and initiatives supporting technological innovation also bolster the growth of this market. Funding programs, tax incentives, and public-private partnerships facilitate the adoption of advanced technologies and encourage continuous innovation.
Finally, the North American market benefits from a robust technological ecosystem, with a strong presence of innovative startups and major industrial players. This dynamic fosters collaboration, knowledge exchange, and acceleration of innovations, positioning North America as a global leader in industry 4.0.
How Are Cloud Solutions Transforming Industry 4.0?
The integration of cloud technologies plays a decisive role in the transformation of industry 4.0. By enabling centralized management and in-depth data analysis, the cloud facilitates the optimization of industrial processes and real-time decision-making.
Cloud solutions offer exceptional flexibility, allowing companies to quickly adapt to changes in demand and adjust their operations accordingly. This agility is essential in a constantly evolving industrial environment, where the ability to react swiftly to new opportunities and challenges is crucial.
Moreover, the cloud allows for better collaboration between different departments and production sites. Teams can access the necessary data and tools from anywhere, thereby fostering smooth communication and effective coordination.
Data security is also enhanced through advanced cloud solutions, which offer robust protection protocols and automated backup mechanisms. This ensures continuity of operations and protects sensitive information from cyber threats.
Finally, the cloud facilitates the integration of emerging technologies such as artificial intelligence and machine learning. By leveraging these tools, companies can analyze large data sets, identify trends, and proactively optimize their processes, thereby increasing their competitiveness in the market.