By establishing itself as a true revolution in the industrial world, lean production redefines management standards by focusing on waste reduction. Originating from the famous Toyota production system, this methodology encompasses a fluid and agile approach where each step becomes essential for an optimal process. Optimizing resources, limiting inventory, and reducing waiting times are all levers that contribute to efficient and streamlined management. Thanks to the active participation of all employees in the hunt for unprofitable tasks, lean fosters team engagement and customer satisfaction while minimizing costs.
Table des matières
ToggleLean Production: A Streamlined Approach
The concept of lean production, often referred to as lean manufacturing, designates a production management method that focuses on optimizing and streamlining resources. It is based on a fundamental principle: producing more with fewer resources. The main objective is to systematically eliminate all types of waste within industrial processes, whether it involves reducing excessive inventory, unnecessary movements, waiting times, or manufacturing defects.
This production philosophy finds its origins in the Toyota production system, developed by Taiichi Ohno and his famous waste-free management method. Thus, lean manufacturing focuses on customer satisfaction while minimizing costs through the implementation of continuous improvements. It is a proactive and collaborative approach that engages every employee in identifying and eliminating unprofitable tasks.
Among the key concepts of lean, we find just-in-time management. This means producing exactly what is necessary, when it is needed, by adjusting production to actual demand and thereby minimizing work-in-progress and unnecessary stock. This approach not only facilitates adaptation to market fluctuations but also significantly improves quality and responsiveness of productions.
The tools of lean are numerous and vary by industry: just-in-time, the 5S, kanban, and the Six Sigma method are among the most widespread. They help streamline production lines, quickly detect inefficiencies, and propose solutions to correct them. Lean is not limited to manufacturing sectors; it also applies to services thanks to its adaptable and flexible method.
One of the essential characteristics of lean is the promotion of team autonomy. Each employee is encouraged to develop their change capabilities, thereby contributing to the overall agility of the company. By eliminating unnecessary waste, a culture of innovation is fostered where every idea counts to continuously improve processes and maximize the value offered to the customer.
The evolution of technologies such as automation and cobots also offers new opportunities to enrich the lean approach. By integrating programmable automata, companies see their production adapt in real-time to ever-changing demands, ensuring quality products with efficient resource use.
Lean production also encourages tailored processes that guarantee the delivery of reliable products while optimizing logistics chain management. The impact of this management method is also felt on the global economy, placing companies in a virtuous circle of responsible and sustainable growth. Explore how these dynamics fit into modern production strategies, like those illustrated in Toyota’s approach.
Adopting lean manufacturing means choosing a long-term vision where agility, efficiency, and innovation dominate, favoring harmonious development aligned with the expectations of the current market.
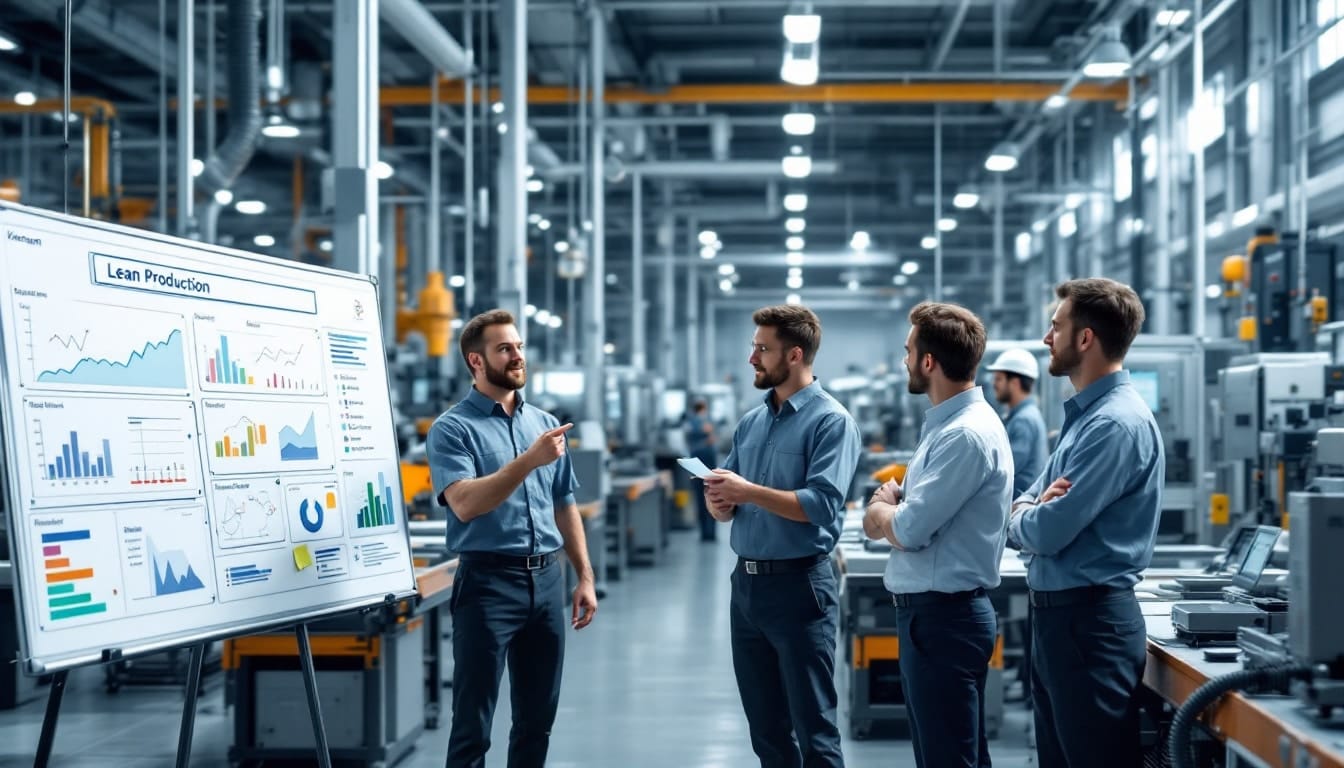
FAQ on Lean Production
Q: What is lean production?
A: Lean production is a management philosophy that seeks to reduce waste in the production process while maximizing value for the customer.
Q: What are the main objectives of lean production?
A: The main objectives of lean production are to reconcile customer satisfaction, team engagement, and the reduction of the company’s overall costs.
Q: How is lean manufacturing implemented?
A: Lean manufacturing is implemented through a detailed analysis of the steps in the industrial process to detect and eliminate waste, whether it be waiting times, waste, or defects.
Q: What is the origin of lean management?
A: The origin of lean management dates back to the Toyota Production System, developed by Taiichi Ohno at Toyota.
Q: What are the benefits of the lean method for a company?
A: The lean method helps a company to reduce its costs by optimizing its resources, improving quality, and increasing its operational agility.