In the dynamic landscape of Industry 4.0, access to digital resources is essential. Technological barriers can hinder the flow of critical information. Understanding these challenges is crucial for optimizing modern supply chains.
Access interruptions, such as restrictions imposed by servers, illustrate existing vulnerabilities. These obstacles can delay the acquisition of crucial data, thereby affecting decision-making. By analyzing the reasons behind these limitations, professionals can better secure their information flows. This enhances the resilience and efficiency of logistical systems in a constantly evolving environment.
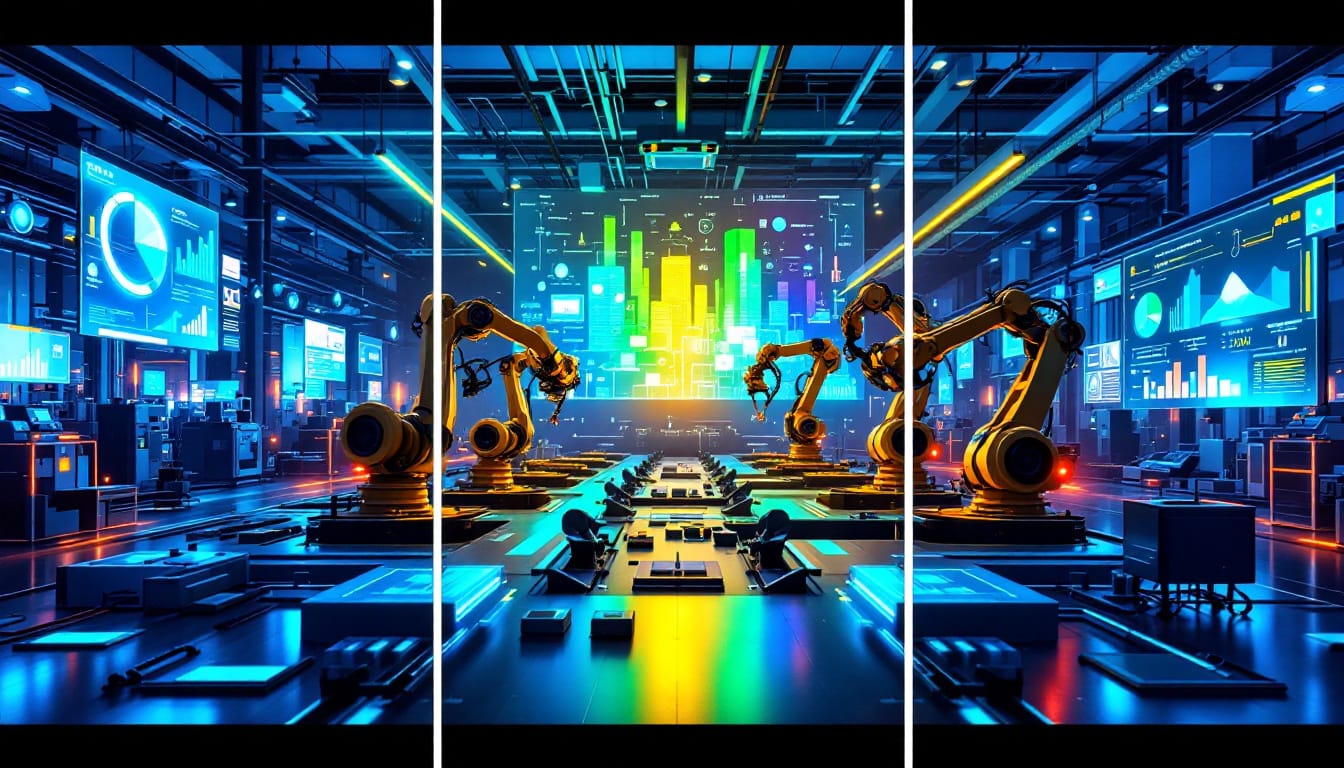
The Internet of Things (IoT) has revolutionized the manufacturing industry 4.0, transforming the way companies manage their operations and optimize their processes. This systematic review is divided into three essential parts: improving connectivity, optimizing production, and securing systems, offering a comprehensive view of the impact of IoT in this context.
Table des matières
ToggleHow does IoT improve connectivity in Industry 4.0?
One of the main advantages of IoT in manufacturing industry 4.0 is the significant improvement in connectivity. Industrial IoT cellular routers play a crucial role in ensuring reliable and fast connectivity between different devices and systems. With these advanced technologies, companies can now monitor their equipment in real-time, gather accurate data, and make informed decisions.
For example, the article on Industrial IoT Cellular Routers highlights the importance of these tools for improved connectivity and edge computing, thus facilitating an industry revolution based on IoT. This increased connectivity not only enables better communication between machines, but also seamless integration with industrial computing systems, promoting a more efficient management of production flows.
Moreover, IoT allows for continuous monitoring of machines, quickly detecting anomalies, thus reducing downtime. This proactive monitoring is essential for maintaining smooth and efficient production, minimizing interruptions and maximizing productivity.
How does IoT optimize industrial production?
IoT plays a decisive role in optimizing industrial production by providing real-time data and advanced analytics. Companies can dynamically adjust their processes to improve efficiency and reduce costs. Customized digital transformation services cater to the specific needs of each company, facilitating the rapid and effective adoption of IoT technologies.
According to the report iiot-optimiser-la-production-industrielle-grace-a-des-services-personnalises-de-transformation-digitale-dans-lindustrie-4-0/”>M-IIoT: Optimize Industrial Production, IoT enables advanced resource management, precise planning, and waste reduction. By integrating smart sensors and automated management systems, companies can monitor every stage of production, identify weak points, and implement continuous improvements.
Another crucial aspect is the use of artificial intelligence (AI) combined with IoT, as described in the article on The Revolution of Industry 4.0. AI analyzes data collected by IoT devices to predict trends, optimize production lines, and anticipate maintenance needs. This synergy between AI and IoT allows companies to become more responsive and adaptive to market challenges.
What are the security challenges related to IoT in Industry 4.0?
With the increase in connectivity and digitalization, security becomes a major concern in Industry 4.0. IoT, while offering numerous benefits, also exposes industrial systems to new threats. It is essential to implement robust measures to protect data and ensure the reliability of operations.
The article How SIM-IoT and Connectivity Security Propel Industry 4.0 highlights the importance of advanced security solutions to protect industrial IoT networks. Companies must adopt strict security protocols, such as data encryption and multi-factor authentication, to prevent unauthorized access and cyberattacks.
Furthermore, the implementation of IoT cognition systems allows for proactive threat detection and rapid response to security incidents. According to the article on Cognitiot by Ranial Systems, these systems offer real-time computing that enhances the resilience of supply chains and prevents disruptions due to cyber threats.
Raising awareness and training teams on best security practices is also crucial. Employees must be informed of potential risks and trained in the secure use of IoT technologies to minimize human vulnerabilities.
What are the benefits of edge computing for Industry 4.0?
Edge computing plays a key role in optimizing IoT systems for Industry 4.0. By processing data locally, close to the source of generation, edge computing reduces latency and improves the speed of decision-making. This allows for increased responsiveness to changes in production and better resource management.
The integration of IoT cognition into edge computing systems, as described in the article on Cognitiot by Ranial Systems, offers advanced computing capabilities that allow for the processing of large amounts of data in real-time. This approach promotes better performance analysis and continuous optimization of industrial processes.
Moreover, edge computing facilitates greater autonomy for smart machines, thus reducing their dependence on centralized systems. This is particularly beneficial in complex industrial environments, where rapid responses and decentralized management of operations are essential for maintaining efficiency and competitiveness.
How does IoT contribute to the resilience of supply chains?
The resilience of supply chains is a major issue for manufacturing industries, especially in a context of globalization and market fluctuations. IoT strengthens this resilience by providing increased visibility and a rapid response capacity to disruptions.
Thanks to IoT sensors, companies can monitor in real-time the status of their inventories, track transport conditions, and anticipate potential delays or issues. This visibility allows for proactive risk management and optimization of logistics flows.
The article on M-IIoT: Optimize Industrial Production emphasizes the importance of IoT for better planning and greater flexibility. By analyzing the collected data, companies can quickly adjust their production strategies, diversify their supply sources, and minimize the impact of disruptions.
Moreover, the artificial intelligence integrated with IoT allows for forecasting market trends and anticipating future needs, thus strengthening the capacity of companies to adapt to changes and maintain their competitiveness. This adaptability is essential for navigating a constantly evolving economic environment.
What are the technological challenges of IoT in Industry 4.0?
Despite its many advantages, the adoption of IoT in Industry 4.0 also presents significant technological challenges. One of the main obstacles is integrating IoT devices with existing systems. Legacy infrastructures may not be compatible with new technologies, requiring additional investments and a redesign of processes.
Another major challenge is managing and analyzing the enormous volumes of data generated by IoT devices. Companies must have robust big data solutions and advanced analytics capabilities to effectively leverage this data. Without adequate analysis, the collected data can become an informational overload rather than a valuable resource.
Moreover, standardization of communication protocols and security standards is essential for ensuring the interoperability and reliability of IoT systems. The absence of uniform standards can lead to compatibility issues and security vulnerabilities, thus compromising the efficiency and safety of operations.
Finally, training and skill development are crucial for the successful adoption of IoT. Employees need to be trained in new technologies and best practices for managing IoT systems to maximize benefits and minimize associated risks.
What are the future developments of IoT in the manufacturing industry?
The future of IoT in the manufacturing industry is promising, with continuous innovations pushing the boundaries of technology and industrial efficiency. Among the emerging developments, the increasing integration of artificial intelligence and machine learning with IoT promises to make industrial systems even more autonomous and intelligent.
Advancements in 5G connectivity will also provide increased capabilities in terms of speed and reliability, facilitating even smoother communication between IoT devices and centralized systems. This will enable more sophisticated applications, such as predictive maintenance and automated management of production lines.
Additionally, the development of augmented reality (AR) and virtual reality (VR) technologies integrated with IoT will open new possibilities for training, maintenance, and optimization of industrial processes. These technologies will offer more intuitive user interfaces and advanced visualization tools, thus enhancing decision-making and responsiveness of teams.
Finally, the growing emphasis on sustainability and energy efficiency will push IoT to play a key role in resource management and in reducing the carbon footprint of industries. IoT devices will be able to monitor and optimize energy consumption, minimizing waste and promoting more eco-friendly production practices.
To learn more about current and future innovations in IoT in Industry 4.0, you can check the latest publications on Cognitiot by Ranial Systems and discover how these technologies are shaping the future of manufacturing production.