Industry 4.0 marks a new era of industrial production, where artificial intelligence and the Internet of Things play a central role. This digital transformation reconfigures production lines, allowing machines not only to operate at their full potential but also to communicate with each other seamlessly. Companies thus benefit from real-time decision-making, increased productivity, and remarkable flexibility in the manufacturing and distribution of their products. By integrating advanced technologies such as Big Data and predictive analytics, Industry 4.0 paves the way for mass customization and an unprecedented level of efficiency in the industrial field.
Industry 4.0, also known as the fourth industrial revolution, is the process of digitizing and interconnecting industrial processes. It utilizes advanced technologies like Internet of Things (IoT), artificial intelligence, and Big Data to transform production, improve productivity, and respond to customer needs with great flexibility.
Smart factories, at the heart of this concept, integrate advanced sensors, embedded software, and robots to collect and analyze data in real-time, allowing for optimized decision-making and self-optimized operations. Industry 4.0 also uses digital twins to simulate and enhance production processes.
This revolution relies on a robust IT infrastructure, often based on cloud computing and edge computing, while paying particular attention to cybersecurity.
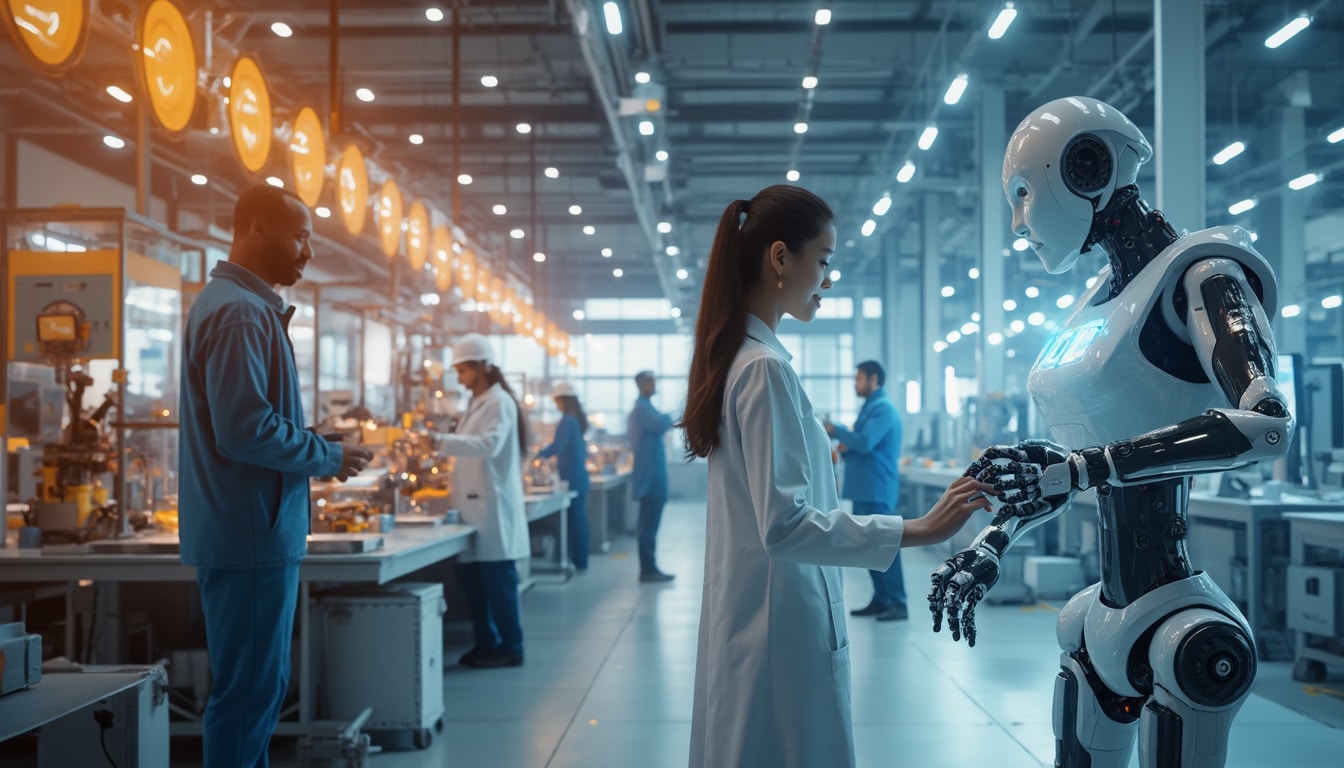
Table des matières
ToggleWhat is Industry 4.0?
Industry 4.0 represents the digital transformation of the manufacturing sector, integrating technologies such as Internet of Things (IoT), artificial intelligence, and Big Data. It is a revolution that offers real-time decision-making, increased productivity, and flexibility never seen before. Unlike previous industrial revolutions, which were marked by the shift to mechanized production or the adoption of electricity, Industry 4.0 focuses on the interconnection of machines and systems to create an environment where smart factories are the norm.
How does Industry 4.0 work?
The key to Industry 4.0 lies in the integration of new technologies. Modern factories use advanced sensors, embedded software, and robots to collect and analyze data in real time. Additional value is gained when these operational data are combined with ERP, supply chain, and customer service data, creating unprecedented levels of visibility and insight. Through increased automation, predictive maintenance, and self-optimization of processes, companies can now respond to customer demands with unprecedented responsiveness. A deep understanding of these technologies is crucial for maximizing the benefits of Industry 4.0.
Key technologies of Industry 4.0
Several technologies propel Industry 4.0 toward a bright future. Cloud computing enables the efficient storage and processing of large amounts of data, helping companies integrate all aspects of their supply chain and production. IoT is another essential component, enabling machines to communicate with each other, collecting valuable data for predictive analytics. Cognitive robotics also represents a leap forward in automating complex tasks. Finally, edge computing ensures that data analysis occurs close to the data source, thereby minimizing latency.