Imaginez une révolution dans le monde de la performance sportive : des semelles personnalisées pour les athlètes olympiques créées en un temps record. C’est désormais possible grâce à la technologie innovante d’Asics, offrant une impression rapide et sur-mesure en moins d’une heure. Découvrez comment cette avancée majeure va changer la donne pour les sportifs de haut niveau.
Table des matières
ToggleUne révolution pour le monde du sport
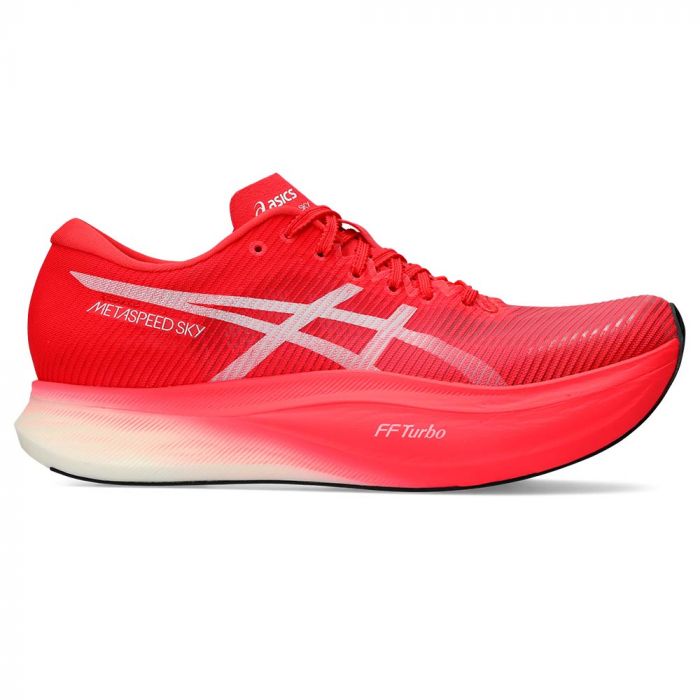
Avec son studio mobile d’impression 3D, Asics bouleverse le monde du sport en permettant d’imprimer des semelles personnalisées en moins d’une heure. Associée à Dassault Systèmes, la multinationale japonaise offre cette innovation aux athlètes de haut niveau, avec l’ambition de la rendre accessible au grand public.
Un partenariat prometteur
À l’occasion des Jeux Olympiques et Paralympiques de Paris 2024, Asics et l’éditeur de logiciels spécialisés dans la conception 3D Dassault Systèmes introduisent cette technologie révolutionnaire. Le studio mobile, logé dans les locaux de Dassault Systèmes à Vélizy (Yvelines), ne manquera pas d’évoluer à mesure que des événements sportifs se profilent.
Les semelles personnalisées de Novak Djokovic
Actuellement, le studio sert à équiper les chaussures de Novak Djokovic, le champion de tennis et partenaire officiel d’Asics. Djokovic utilise ces semelles personnalisées quasi-quotidiennement en période de match. Selon Mitsuyuki Tominaga, président-directeur général d’Asics, cette innovation aide à prévenir les blessures en corrigeant les points d’appui des athlètes.
Un processus simple et rapide
Le processus commence par un scan des pieds nus de l’athlète via une application mobile développée par Asics. Cette application prend quatre photos pour mesurer chaque pied sous tous les angles, grâce à l’intelligence artificielle. Le scan est ensuite envoyé à un logiciel développé par Dassault Systèmes pour traitement automatique. Le résultat est un nuage de points détaillant la géométrie et les points d’appui du pied.
La fabrication des semelles en 3D
Les données sont ensuite utilisées pour modéliser les semelles en polymère, qui sont fabriquées dans une imprimante 3D. Le processus complet, de la numérisation à la production, est supervisé grâce au jumeau numérique de l’unité mobile. Ce travail de modélisation, sur lequel Asics et Dassault Systèmes ont collaboré pendant 18 mois, représente une véritable avancée technique.
Une personnalisation pour la performance
Une fois modélisée, la semelle est fabriquée, séchée et chauffée pour assurer une durabilité optimale. Ce processus permet également de fabriquer des sandales de récupération, très demandées par les athlètes. Asics a déjà vendu 30 000 exemplaires de ces sandales, bien que la date de mise en vente des semelles sur-mesure ne soit pas encore annoncée.
- Scan rapide et précis avec une application mobile
- Traitement des données par un logiciel avancé
- Fabrication en moins d’une heure grâce à l’impression 3D
Un marché en pleine évolution
Le marché des semelles personnalisées par impression 3D est en pleine expansion. Des entreprises comme Adidas explorent également cette avenue pour offrir toujours plus de personnalisation. Bien que le défi soit grand, la collaboration entre Asics et Dassault Systèmes prouve que l’innovation constante peut ouvrir de nouvelles perspectives pour les athlètes et le grand public.
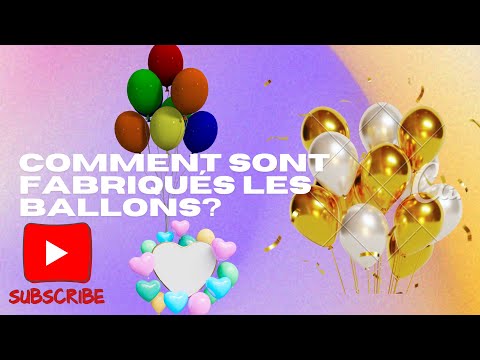
Quand je vois et j'écoute ça, je pense au paillasson en effet.
— Léopold Saroyan (@cf_deTartas) April 3, 2024
Un paillasson qui en a vu passer des semelles voulant tant bien que mal en ressortir propres.
C'est exactement l'impression que donne cet individu qui représente tout sauf la France.#LouisBoyard https://t.co/2hoVnspT6x